India is the world’s second-largest manufacturer of bricks. Our country produces 10% of all the bricks manufactured globally and there are over 1,40,00 brick making units spread across the nation. While there have been plenty of new-age building materials, bricks never go out of style or popularity. Here, in today’s article, we take you behind-the-scenes of brick making – showing you how bricks are manufactured and their incredible benefits.
How are Clay Bricks made in India?
The brick manufacturing process consists of the following steps.
1. Preparation of Raw Materials
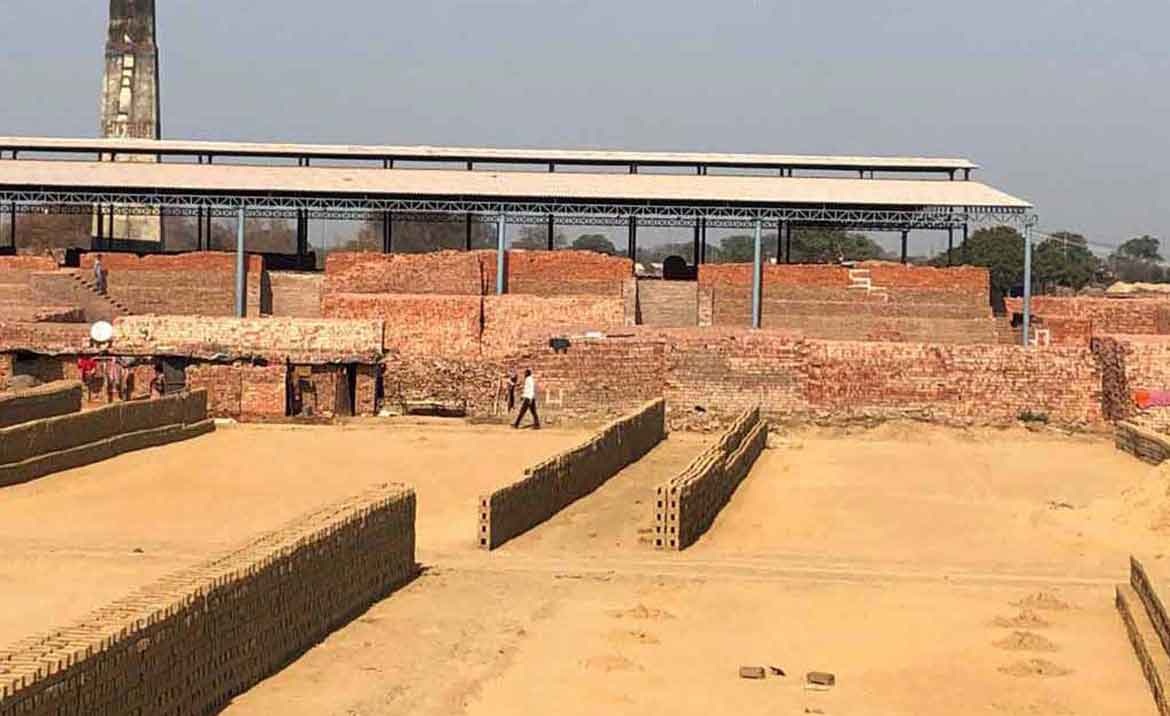
In this stage, all the raw materials required for brick making are prepared. The first step involves getting the soil ready. It’s removed from impurities like pebbles, stones, and other vegetation matter. Once it is clear of all impurities, it’s left out in the sun for a few months. This step is known as weathering.
Once the soil is ready, it is mixed with other materials to prepare the right earth needed for making clay bricks. Post this stage, the soil goes through various processes like watering, breaking, and kneading to get it ready for the next step.
2. Moulding
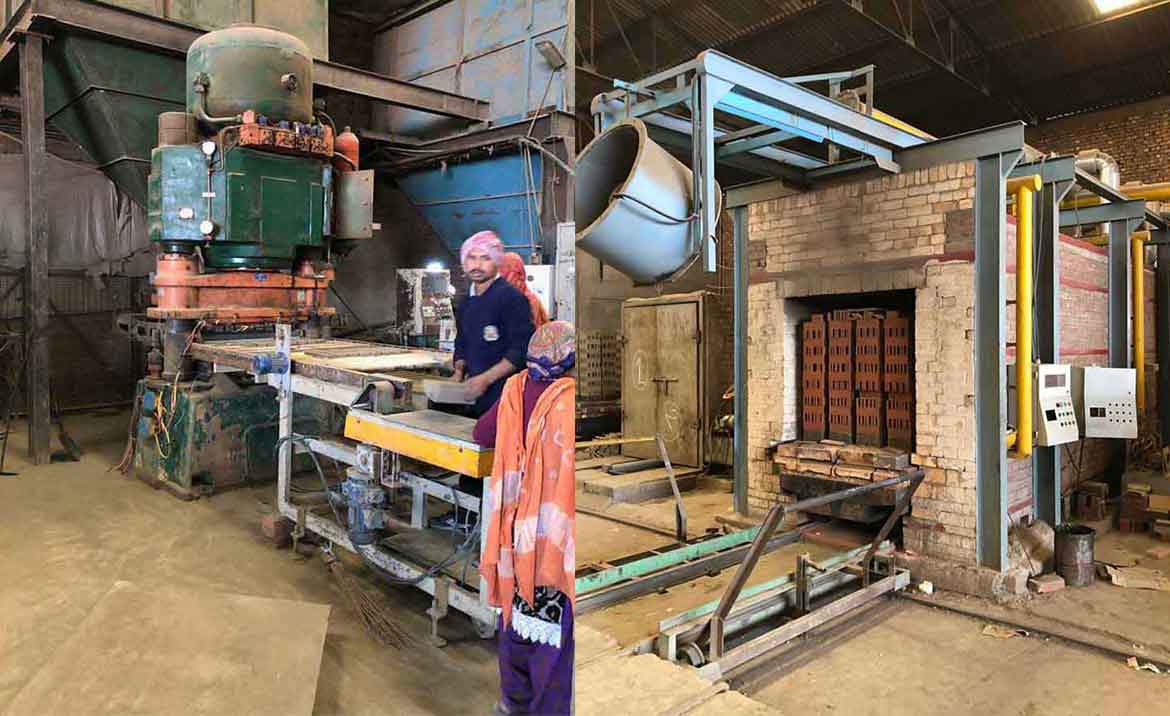
Earlier, brick makers used wooden moulds sanded with fine sand for shaping the bricks. Today, there are several modern moulds made out of steel, etc. The two major types of moulding include:
Hand Moulding – Here, the prepared clay is inserted into the mould by hand. Brickmakers ensure that the clay fills all corners of the mould. Extra clay is removed using a wireframe. Once the clay has been properly filled, the mould is lifted from the ground, and the raw brick is left back in the ground.
Machine Moulding – Hand moulding is a time-consuming process. Hence, machines are used in the moulding stage to quicken the brick making process. There are two major types of machines used:
Plastic Clay Machines - Here, the clay is mixed to a state similar to molten plastic. The prepared clay is injected into rectangular openings that are equal to the length and breadth of the brick. Finally, the raw bricks are cut into the desired dimensions using wireframes.
Dry Clay Machines - Here, dry clay in powder form is filled into moulds using machines. These moulds are then exposed to high pressure to form well-shaped raw bricks.
3. Drying
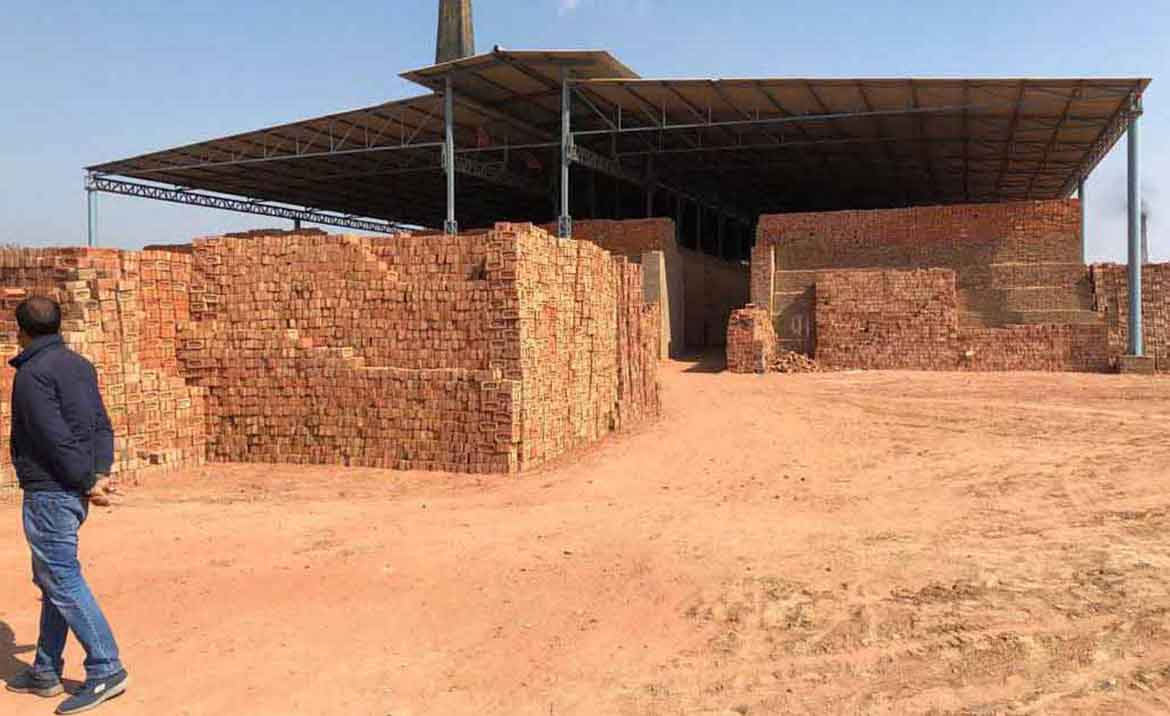
Drying is one of the major and also the time-consuming steps in brick making. Raw bricks are let out dry to eliminate cracks. If bricks are burnt before they are completely dry, it can lead to cracks. Drying ensures that all moisture is eliminated from the raw brick. Drying is essential to increase the durability and strength of raw bricks.
Generally, raw bricks are dried by arranging them in lines in brick sheds that have open sides. This process takes around 7 to 14 days, depending on the weather conditions.
4. Burning or Firing
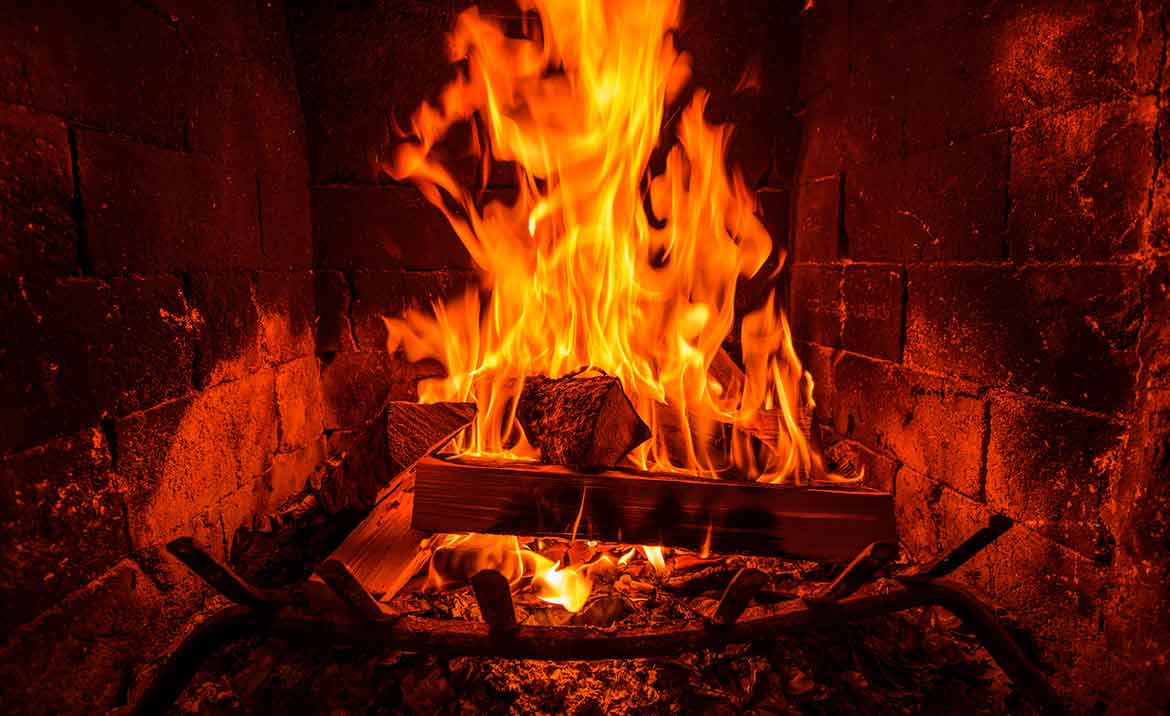
Once the bricks are dried completely, they are burnt to high temperatures in large furnaces. In India, clay bricks are fired using two different methods:
- Clamp burning also known as Pazawah
- Kiln burning also known as Bhatta
Burning of bricks is a multi-step process. The first stage is water-smoking or pre-heating. It removes all the leftover water in the brick. Next comes the actual firing. Here, clay bricks are burnt using a chemical process. The final stage is cooling. The bricks should not be brought to room temperatures instantly. Rather, they have to be cooled down slowly and steadily.
That’s it. These are the four major steps in brick making. Punjab, Gujarat, Tamil Nadu, Haryana, and Uttar Pradesh are the major brick producing states in the country. Brick making in India remains a traditional practice, involving manual labour.
Now that we’ve seen the brick making process, let’s see the major benefits of clay brick making.
Aesthetic Appeal
It’s no surprise that bricks have been used since the dawn of civilization for construction. By altering various factors like – clay compositions, kiln atmosphere, the firing temperature – the output colour of the brick varies.
Contrary to popular assumption, bricks are available in a wide variety of colours ranging from dark reds and browns to even whites, greys, and blacks.
Thermal and Acoustic Insulation
Bricks offer better thermal and acoustic insulation compared to other building materials. Bricks absorb and release heat slowly, thereby keeping the house warm during the night and cool during the day. Apart from heat insulation, bricks also offer acoustic insulation. The thick nature of the brick means that noise transmission is cut down significantly, thereby filtering out street noises.
Zero Maintenance
One of the biggest benefits of clay bricks is that it’s zero maintenance. With clay bricks, you don’t have to worry about pest infestations, fading, peeling, splitting, rusting, warping, denting and rotting. A brick wall lasts for years to come without any extra maintenance.
Fire Resistant
Clay bricks offer natural fire resistance. This gives an extra sense of security and peace of mind to homeowners.
Versatile
Clay bricks can be used for a wide range of applications, from single-storey homes to multiple-storey skyscrapers. Besides, clay bricks can be shaped into different sizes to suit specific needs.
Wrapping Up
Purchase Clay Bricks at the Best Costs from leading Clay Bricks Suppliers in Gujarat, India. Décor Cera is one of the leading Clay Bricks suppliers in Gujarat, India. We ship our products all over the country. Get in touch with our team to get a free price quotation.